Expertising bearing failures
This is a study case about analysing the source of the problem on a bearing failure.
Introduction
In cases of damaged bearings, it is sometimes difficult for users to establish exactly where the problem lies in a system comprising a number of parts subject to both mechanical and electrical stresses. In practice, visual inspections may at first suggest that the problem is mechanical in nature (vibrations, load, lubrication, settings, etc.), but failures can have other causes.
A typical example is that of a tapered roller bearing fitted on the wheel hub of a rubber-tyred rail vehicle that is showing signs of abnormal wear and tear after 250,000 km in service (Figure 1).
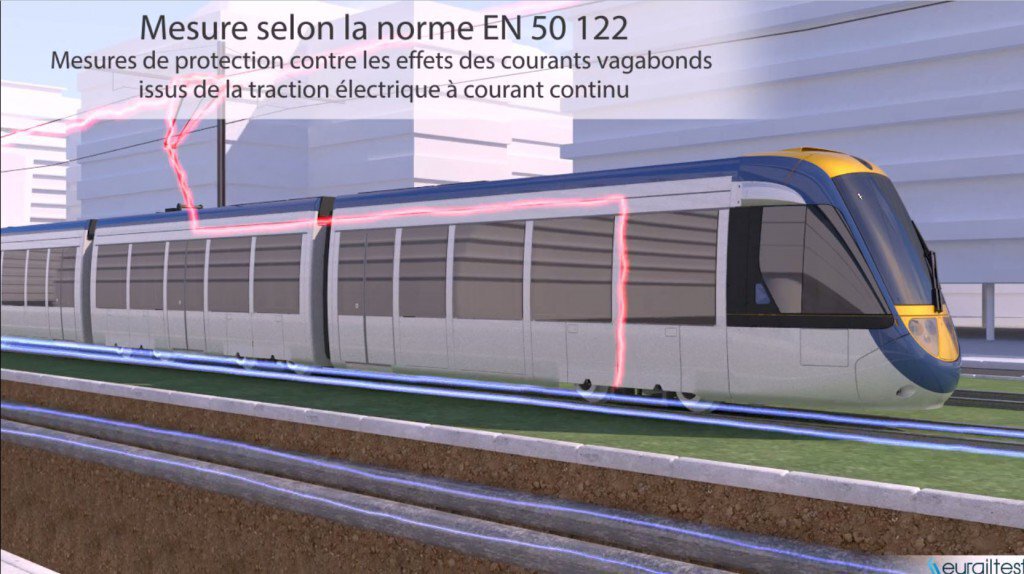
Action
In addition to the “normal” tests on materials (hardness tests, spectrometry, etc.), bearings are submitted to morphological analysis using both macroscopic (binocular microscopes) and microscopic techniques (scanning electron microscopes) to examine their most typical defects. To supplement these examinations, micro-sections are taken from some parts of the bearing in order to examine specific metallurgical phenomena. This process is followed by targeted micro-hardness measurements.
However, to channel analyses in the right direction and suggest possible avenues worth considering or investigating, it is necessary to be fully aware of the conditions under which the rolling stock concerned is operated.
Expert analysis
The inner and outer bearing race surfaces show signs of spalling, at times over sizeable areas ( >1 mm), and there are some defects that are circular in shape that closely resemble “melt holes” (Figure 3).
In order to identify more precisely the characteristics of each individual type of defect, parts are further submitted to microscopic examination using a SEM (scanning electron microscope). Examination of a “melt hole” type defect under heavy magnification (X 2900) reveals the existence of dendrites at the surface, which confirms that there are spots where the metal has melted. Similar defects are found on the surface of the tapered rollers (Figure 4).
In the particular case mentioned here, there are no traces of any defects in the material that could be connected with the wear damage noted.
The next stage is to take a cross section of the bearing at “melt hole” level. The section examined shows the tempered martensitic structure, with globular carbides, commonly found in bearing steels. However, there are also crescent-shaped white areas on the raceway surface. These are a sign of martensitic hardening caused by the friction generated when loose particles are crushed or of surface defects resulting from local melting. Defects of this type are related to the presence of electric currents and explain the mechanical spalling also observed on the bearing. In practice, in addition to the heat-affected area, melt holes create particles that break loose and are subsequently crushed between the contact surfaces, thus triggering a mechanical process (martensitic hardening), which rapidly degenerates into “mechanical” spalling.
Given the size of the defect, it is possible to carry out Vickers hardness tests HV 0.1, to more clearly define the characteristics of the different areas apparent (Figure 5).
The white area shows very high hardness levels (work hardening). By contrast, the darker rim edging the lighter areas, where there is a relative drop in hardness levels, is more characteristic of a heat-related issue.
Conclusion
From the examination of the material, it was possible to rule out any assumption of defects ascribable to a supply problem.
In the particular case under consideration, the melt holes examined can only have been caused by an electrical phenomenon resulting from the presence of a strong current. Mechanical phenomena can therefore be excluded.
In the case of rubber-tyred rolling stock, traction return current and bogie bonding are achieved by means of “negative polarity” and “bonding” contact shoes that slide against the steel rail. If the contact between these shoes and the rail is bad, there can be differences in potential between the electrical bond and the traction return current. This phenomenon may occur when the steel wheel comes into contact with the rail (especially when negotiating points and crossings), with the result that undesirable electric currents may transit through the bearings.
These conclusions will enable the user to take faster and more effective remedial action.